By Jake Bourn | Mar 21, 2025 | OpenVision, CUI
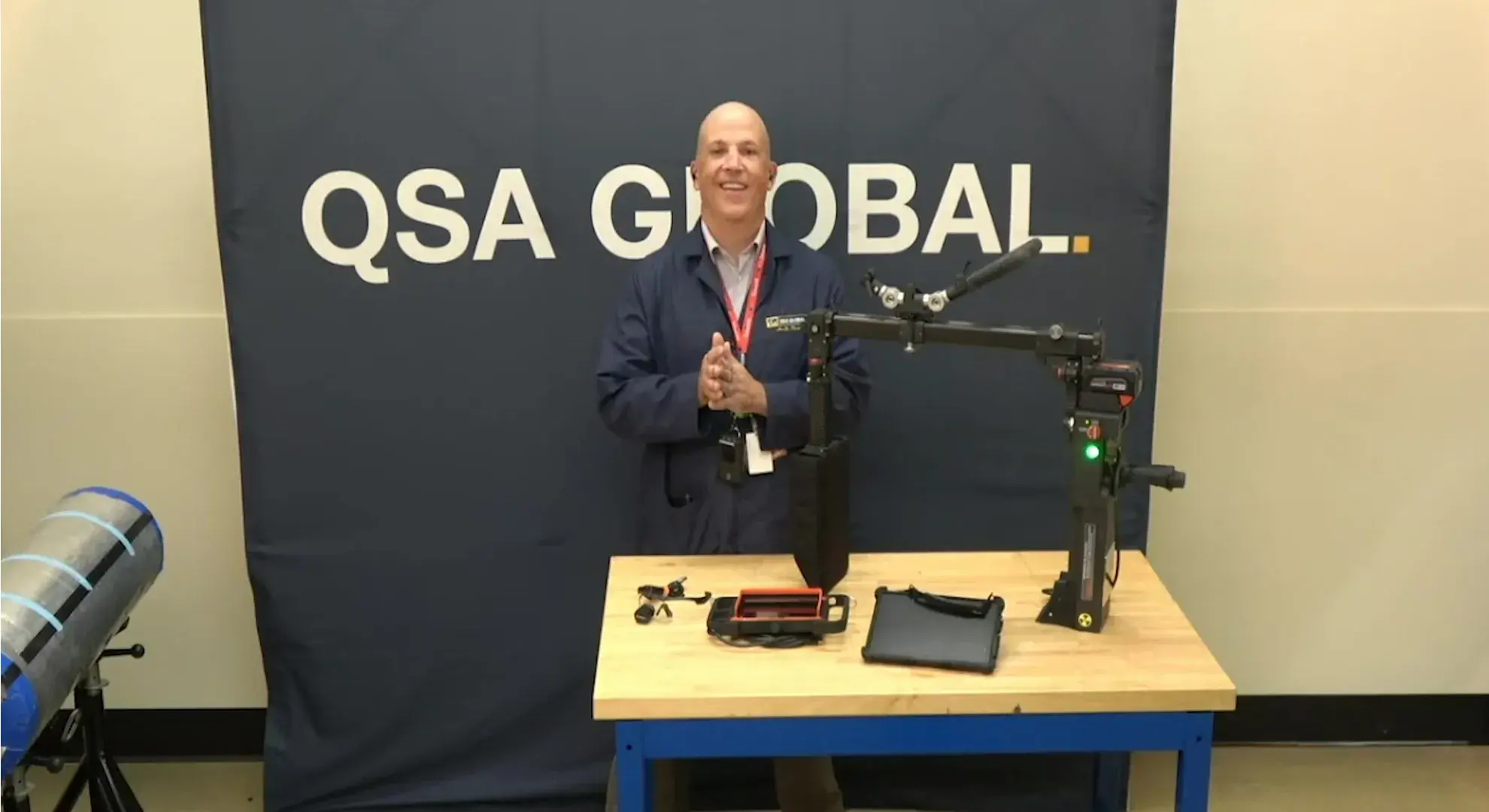
By Jake Bourn | Mar 21, 2025 | OpenVision, CUI
Corrosion Under Insulation (CUI) remains a persistent and expensive challenge in the process piping industry. In refineries, petrochemical plants, and offshore platforms, insulation often conceals degradation until it is advanced, posing safety risks, impacting reliability, and driving up maintenance costs. Asset owners and inspection teams need reliable methods to screen for CUI without the time, labor, and expense of full insulation removal.
Real-time radiography is one method that supports efficient screening of insulated piping. It enables inspectors to identify early signs of corrosion with minimal disruption, using portable X-ray systems that provide immediate imaging feedback. This post outlines how the method works, where it fits into inspection programs, and what to consider during implementation.
Handheld real-time radiography systems use a low-energy X-ray source and a digital detector to provide a live view of internal piping. The display updates dynamically as the operator moves the device, allowing continuous scanning. Operators can capture video or still images for documentation.
Unlike traditional radiography, this method does not require film processing or large-scale setup. The image output can be viewed using wired monitors, integrated glasses, or wireless displays.
Real-time radiography is used as a first-pass screening tool to identify corrosion-susceptible inventory (CSI) across long runs of insulated piping. Systems like OpenVision™ DX allow technicians to move quickly along the pipe surface, visually identifying signs of corrosion such as blistering, internal scale, or insulation deformation without removing insulation.
The basic workflow includes:
Corrosion under insulation is typically assessed using multiple non-destructive testing (NDT) methods. Each has specific use cases, advantages, and limitations. The most common methods include:
Real-time radiography is used early in the process to screen large areas efficiently and identify where other tools should be applied. While it does not provide quantitative data, it helps prioritize follow-up inspections where more precise measurements are needed [2] [3]
When deploying real-time radiography, consider the following:
Real-time radiography is a practical screening method for identifying corrosion under insulation across insulated piping systems. It allows inspection teams to cover large areas quickly, detect signs of damage without removing insulation, and determine where further testing is required.
This method should be integrated into a structured inspection strategy that includes clear procedures for data capture, follow-up evaluation, and training. When used alongside other NDT tools, real-time radiography helps prioritize inspection resources and supports more efficient CUI management.
[1] Inspectioneering. (1996). Inspection Techniques for Detection of CUI. Inspectioneering Journal, November Issue.
[2] ASNT. (2015). Nondestructive Testing Handbook, Volume 5: Radiographic Testing. American Society for Nondestructive Testing.
[3] API. (2014). API RP 583: Corrosion Under Insulation and Fireproofing (CUI/F). American Petroleum Institute.
For oil and gas, power generation, and petrochemical facilities, Corrosion Under Insulation (CUI) remains one of the most costly and difficult ...
Corrosion Under Insulation (CUI) remains one of the most expensive and unpredictable challenges asset owners face, with industry estimates ...