By Jake Bourn | Jan 06, 2025 | CUI
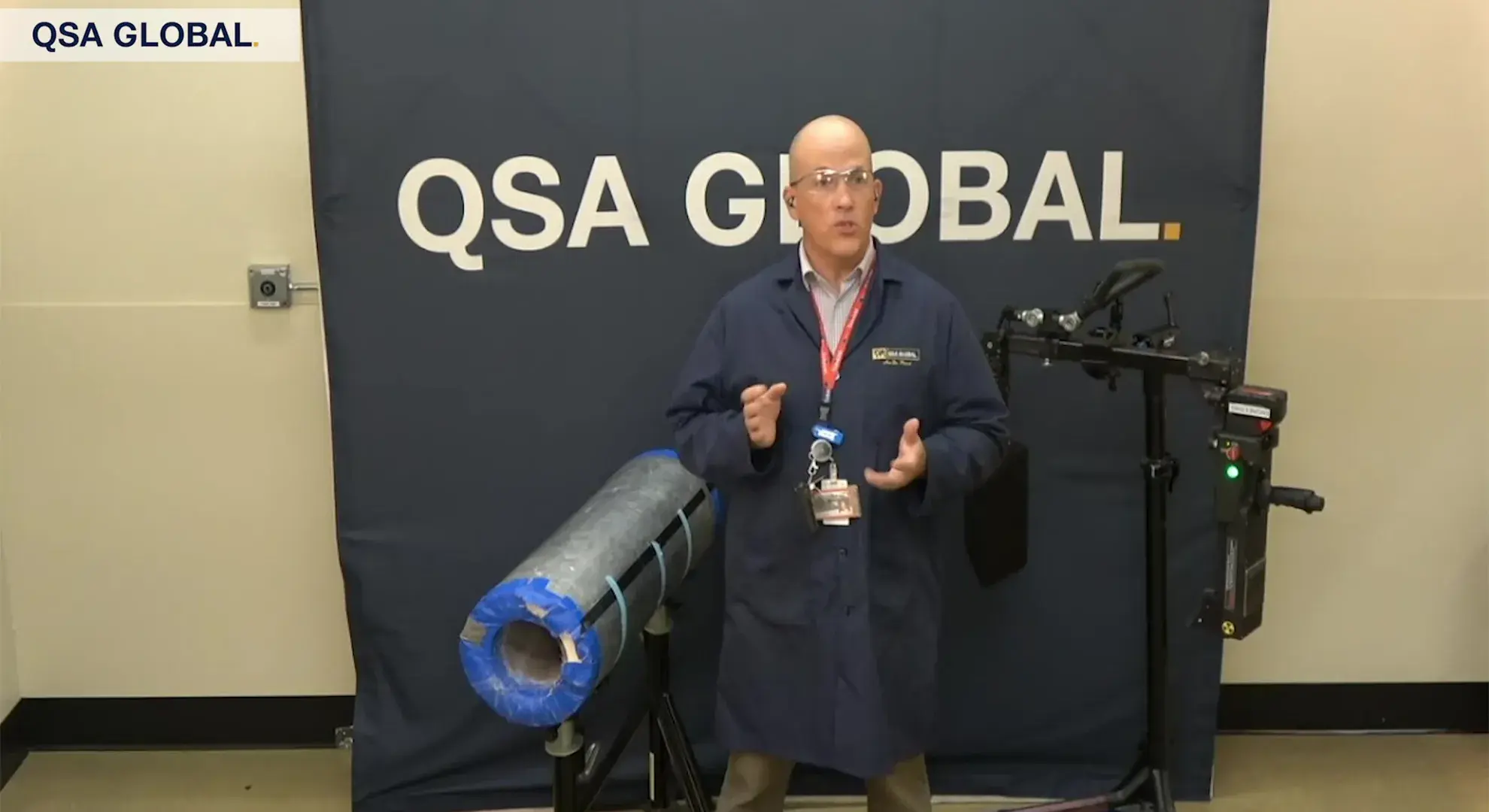
By Jake Bourn | Jan 06, 2025 | CUI
Corrosion Under Insulation (CUI) remains one of the most expensive and unpredictable challenges asset owners face, with industry estimates suggesting CUI-related maintenance costs exceed $2.5 billion annually across the energy sector. Despite decades of experience, there is still no universal strategy to manage it efficiently. Companies continue to rely on costly and reactive methods that do little to prevent long-term damage. Without a shift in approach, maintenance costs will keep rising, and infrastructure integrity will remain at risk.
In many regions, asset owners strip insulation, even when it is still in good condition, to check for corrosion. A typical insulation removal and reinstallation project on a moderate-sized process unit can cost $50,000-$150,000, not including the operational downtime required. This approach is expensive and inefficient.
Key issues with stripping insulation to check for corrosion:
Millions are spent annually stripping insulation without clear data to justify the effort. .
Companies often lack metrics on find rates and coating damage.
Decision-making is based on assumptions rather than measurable risk.
Operational disruptions occur during unnecessary maintenance activities.
Many operators rely heavily on NDT techniques, such as radiography and ultrasonics, to detect CUI. While these methods are critical for assessing structural integrity, they only reveal damage after it has occurred. When damage is discovered after it has progressed, repair costs are typically 3-5 times higher than preventative measures would have been.
NDT inspections can determine:
Whether damage or degradation has occurred.
The remaining condition of the asset.
However, it does not prevent degradation from happening in the first place.
Aging infrastructure makes CUI management even more difficult. Factors that increase risk:
Deteriorating piping and unmaintained sheathing allow more moisture intrusion.
Insulation degrades over time, making assets more susceptible.
Unaddressed gaps and separations continue to expand the number of at-risk assets.
The longer maintenance is deferred, the greater the burden on inspection programs.
When inspection strategies rely on reactive measures, asset owners end up managing problems instead of preventing them. A structured approach using engineering rigor and data-driven decisions is necessary to control costs and reduce the risks associated with CUI.
Key steps to improve CUI management:
Implement a risk-based approach to identify high-priority areas for inspection and targeted insulation removal..
Use predictive analytics and monitoring tools to detect potential issues early.
Focus on preventive maintenance rather than reactive inspection.
By shifting to a data-driven approach, asset owners can reduce unnecessary costs, extend the life of their infrastructure, and minimize unexpected failures. This industry-wide challenge requires new thinking about how we approach CUI management.
Evaluate whether your inspection program uses predictive data to prioritize maintenance or still relies on costly, outdated methods. The future of effective CUI management lies not in doing more inspections, but in making smarter decisions about where and when to deploy your resources.
Corrosion Under Insulation (CUI) remains a persistent and expensive challenge in the process piping industry. In refineries, petrochemical plants, ...
For oil and gas, power generation, and petrochemical facilities, Corrosion Under Insulation (CUI) remains one of the most costly and difficult ...